- Interview
vol.01
Having the freedom to design every texture you can think of; The organic-inorganic hybrid material jesmonite and how it is the key to optimized production quantities
In the interview series “Dive into Material,” MTRL collects information on a variety of different materials, finds creators from all over who are in search of new and unknown materials, and describes for them the appeal of each material while providing tips on how to use them.
Dive into Material #1
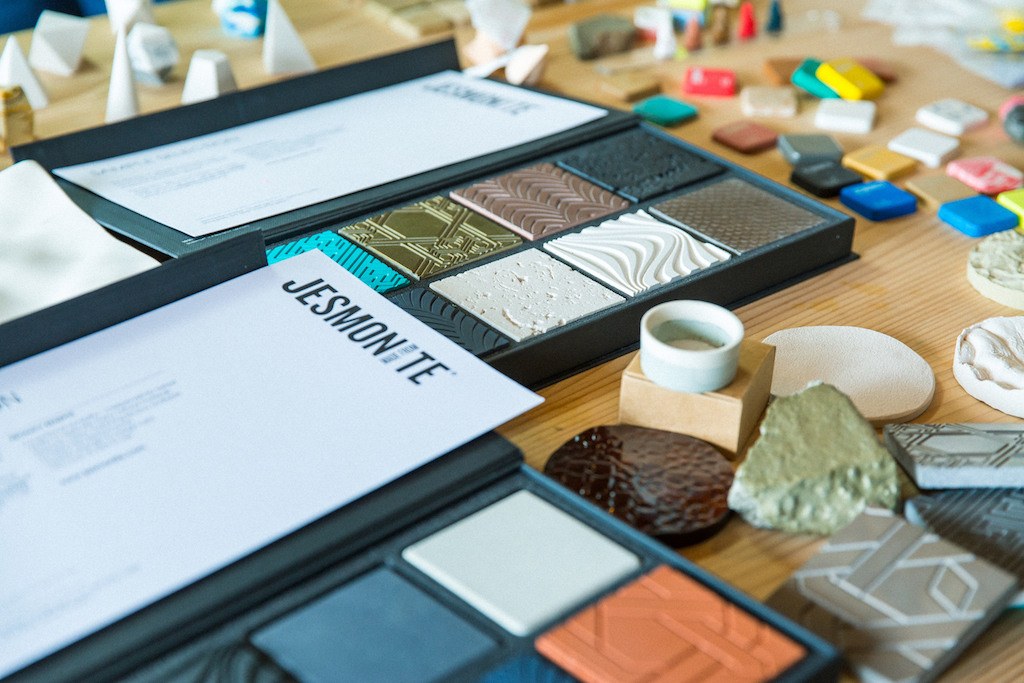
MTRL KYOTO works to establish connections between creators and material makers by holding various material exhibitions, conducting workshops, and more. As a part of these efforts, “Dive into Material” is a movement launched as a response to the countless creators expressing an interest in learning more about how to use the materials they encountered at an exhibition.
The highly noteworthy subject of our first interview is the material jesmonite. Known as a “chameleon material” due to its ability to exhibit a broad range of textures, jesmonite is used to create a wide variety of three-dimensional works, including art, sculptures, furniture, interior design pieces, accessories, and architecture.
In this interview, head of promotion Hiroko Matsumoto shows MTRL Kyoto’s Kousuke Kinoshita some examples of jesmonite’s applications while passing on tips for how to use it.
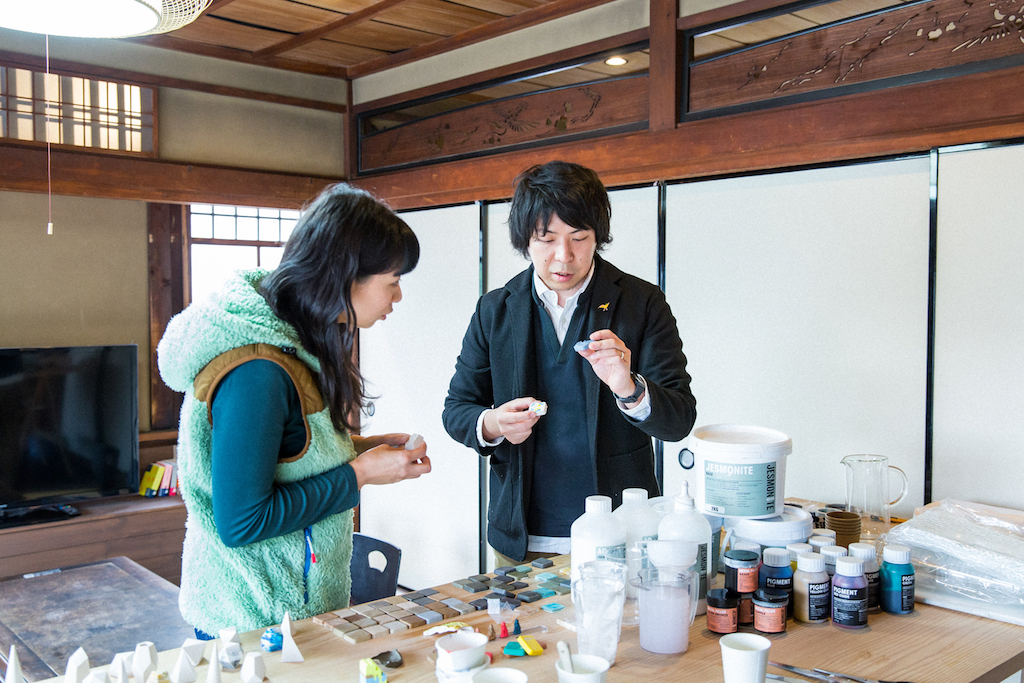
A hybrid material born in the United Kingdom
–Thank you for preparing such a wide variety of samples for this interview. The arrangement laid out on the desk are enough to elicit a chorus of excited comments and conversations along the lines of “Wow! It’s beautiful!” and “How do you make something like this?” You can really feel how these things have the power to connect people to one another.
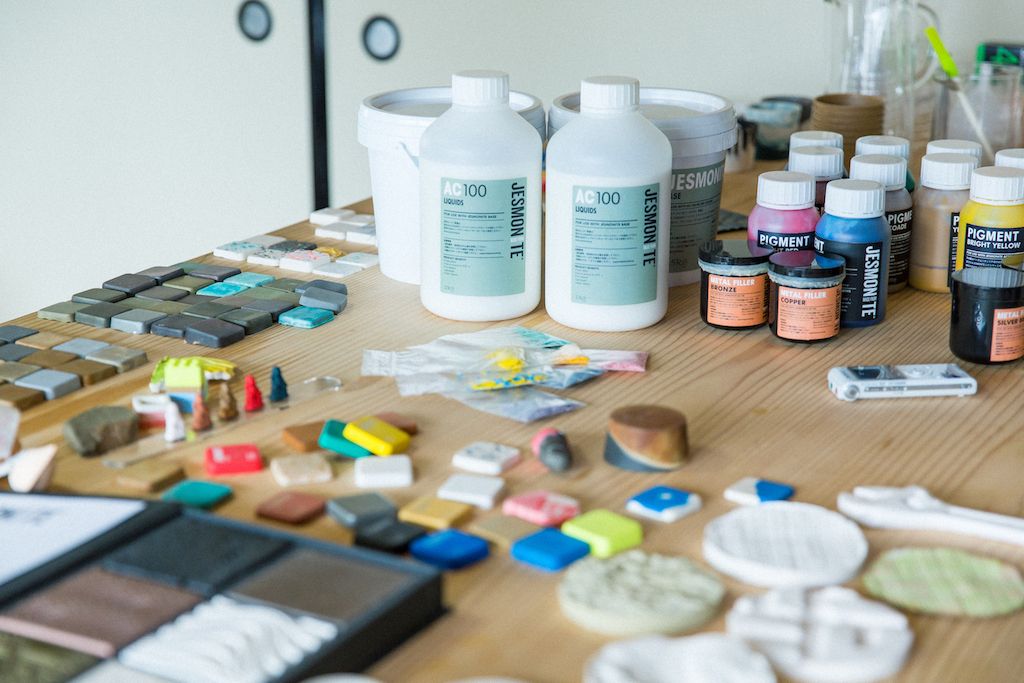
I understand that jesmonite is able to exhibit a broad range of textures, and I know that its fascinating properties have attracted a lot of attention in recent years, but where exactly does jesmonite come from?
Matsumoto: To provide some historical background, jesmonite was developed in 1984 by Peter Hawkins of the English company Jesmonite Ltd. as a substitute material that is safer than FRP (fiber-reinforced plastic) and lighter than concrete. FRP is a material prized for being low-cost, lightweight, and highly durable. For many years it was used to construct unit baths, ship bodies, amusement parks, and various other recreational equipment. However, the significant strain it places on both the human body and the environment has come to be viewed as a problem.
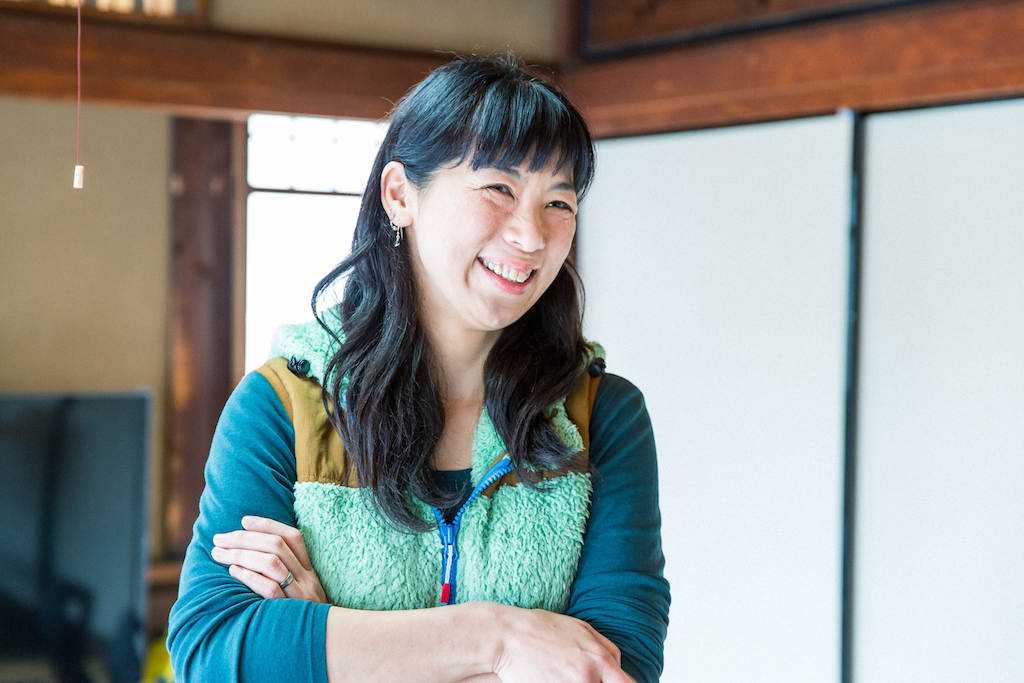
Matsumoto: With this in mind, jesmonite was invented as a safe water-based resin that did not make use of organic solvents (a general term for organic compounds capable of dissolving other substances). As a material that causes minimal harm to the human body and is friendly to the environment, jesmonite has been used as a major material in the creation of works such as sculptures, artwork, and even archeological and paleontological models for over 30 years.
In recent years it has also been increasingly put to use for a variety of new categories, including product design and furniture design.
In spite of its 30 years of history, the word “jesmonite” has only reached Japanese ears very recently. As a safe and eco-friendly material, it seems a good thing that jesmonite’s influence is spreading far and wide. So why is its existence still barely known?
Matsumoto: My best guess is that this is because of the strict, long-standing restrictions on organic solvents enforced in Europe and America, whereas Japan does not adopt rigid limitations on the development of new resins.
I was introduced to jesmonite by an artist who had just returned from the United Kingdom. This safe, high-strength, and easy-to-manipulate material left quite the impression on me.
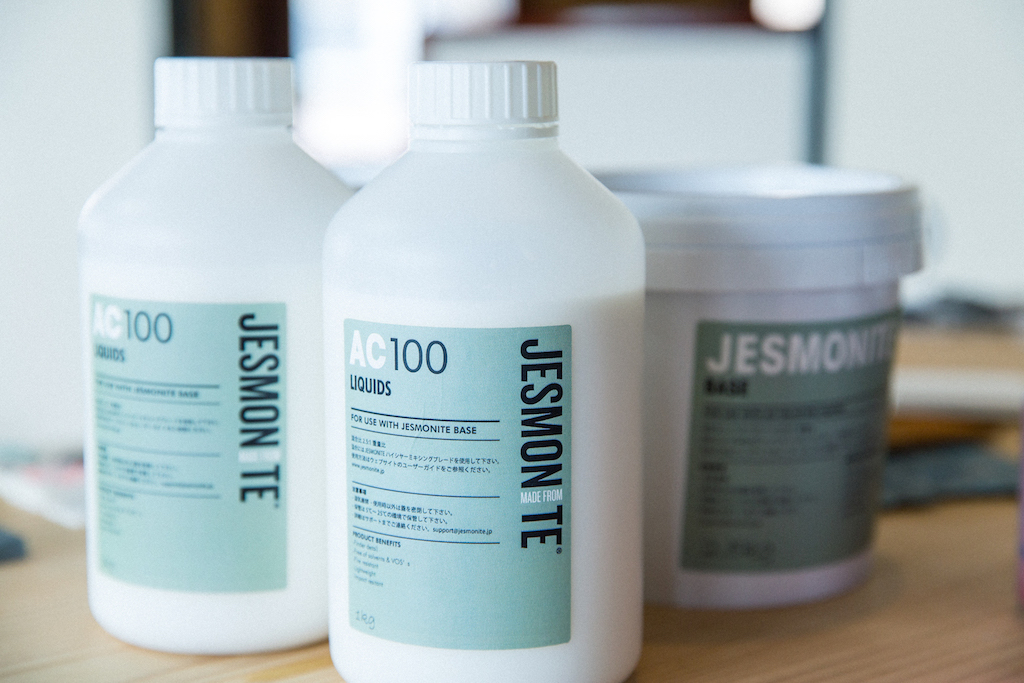
–Ordinarily, organic solvents produce intense odors that require the user to make special considerations about the surrounding area, and in order to reduce the harm it can cause to the human body, FRP must be handle in a very well-ventilated facility during the molding process. Because organic solvents are not well suited for contact with the human body, there are some artists who give up on using them in their creations altogether. Jesmonite, however, can be easily used to create works for cafes and other wide open spaces, making it a highly worthwhile material for creators.
Matsumoto: Thank you. Jesmonite is an organic-inorganic hybrid material made from a mixture of a water-based acrylic resin liquid and a reactive mineral base. Organic liquid enters the gaps in the solidified structure that results from the mineral’s reaction to moisture, resulting in a new material with an even sturdier construction.
–Interesting. So it has the characteristics of both organic and inorganic materials. In spite of being a type of resin, it has a muted rock-like texture without the glossiness of plastic. Its texture looks a bit like that of bisque pottery.
Basic tips and directions to keep in mind
–Next, I would like to actually mold something with jesmonite while hearing about the guidelines and tricks there are to using the material.
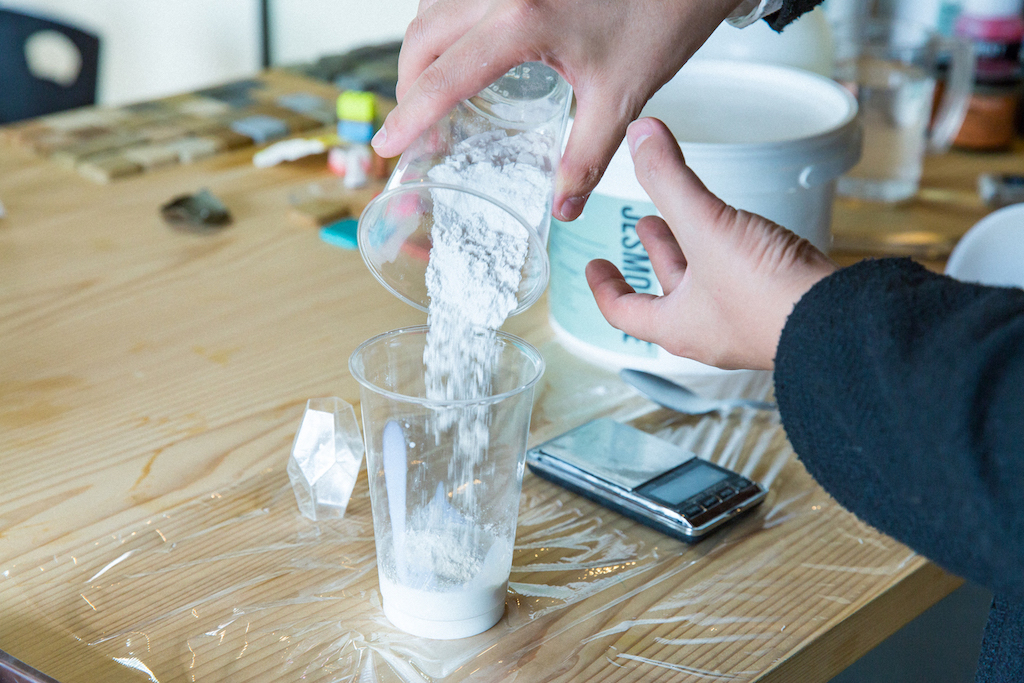
–Jesmonite molds are formed from the mixture of a liquid and a powdery base. Is there a proper ratio to observe with these components?
Matsumoto: The standard liquid-to-base ratio is 1:2.5.
–So, just like with baking, if you don’t measure it out exactly right, it won’t solidify?
Matsumoto: In fact, one of the most incredible aspects of jesmonite is that there is a fair degree of leeway in the component ratio. Even when made with a ratio of 1:2 or 1:3, it will still solidify. Those who want to increase its viscosity add a higher concentration of base for a ratio of 1:3, and those interested in increasing its liquidity use a ratio of 1:2.
–So you’re saying that you can make fine adjustments according to what you want to sculpt? How do you decide what amounts to mix?
Matsumoto: Jesmonite has a specific gravity of 1.75, meaning that, when making a 100cc solid mold, you need to prepare 100cc x 1.75 = 175g (6.2 oz) of jesmonite. Since 175g is the weight of the liquid and base mixture, divide it according to the ratio of 1:2.5 to get 50g of liquid and 125g of base.
*Calculation Sheet
–What should you keep in mind when mixing the components together?
Matsumoto: Although the jesmonite will solidify regardless of which component you start with and which one you mix in, through experience you will find that starting with the base and mixing in the liquid reduces lumpiness and creates a prettier final product. Also, it’s important to blend the mixture thoroughly using a spatula instead of a spoon.
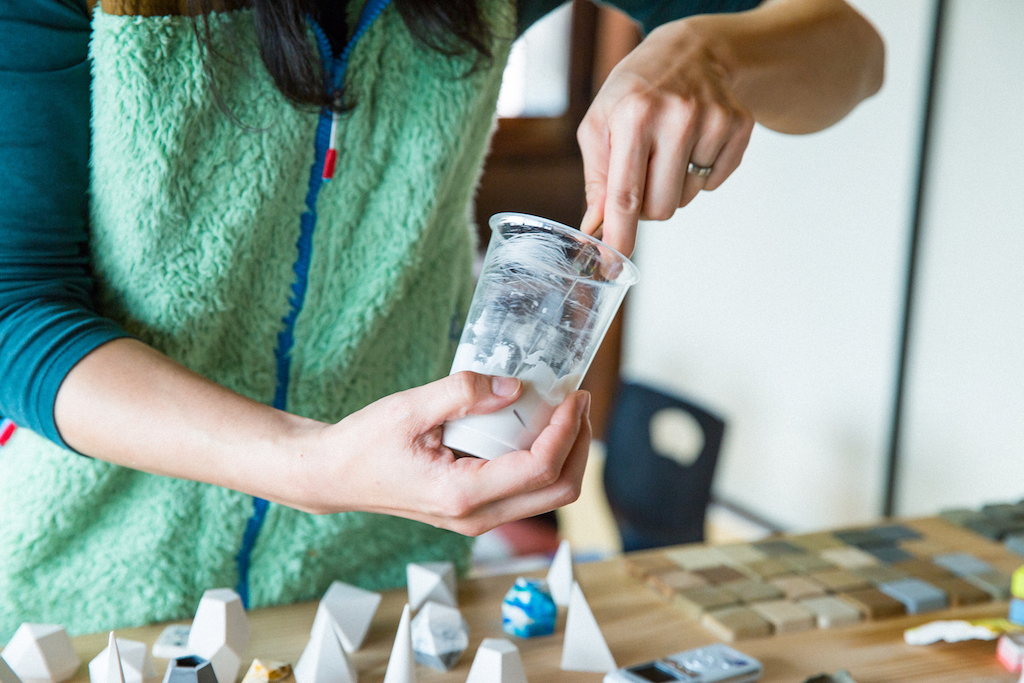
Matsumoto: The mixture will start to harden about 10-20 minutes after you start mixing, so you should try to work as quickly as possible. A warm and dry room is the ideal environment for process. Depending on the exact temperature and humidity, the mixture tends to start hardening more slowly in the winter and more rapidly in the summer. Right now we are mixing by hand, but when dealing with bulk quantities, we use a hand drill with a blade attachment as our stirring tool.
–How much time should I spend mixing?
Matsumoto: It’s best to stir persistently for 1-2 minutes after it becomes viscous. If there are any clumps left in it, its surface will be uneven when it hardens.
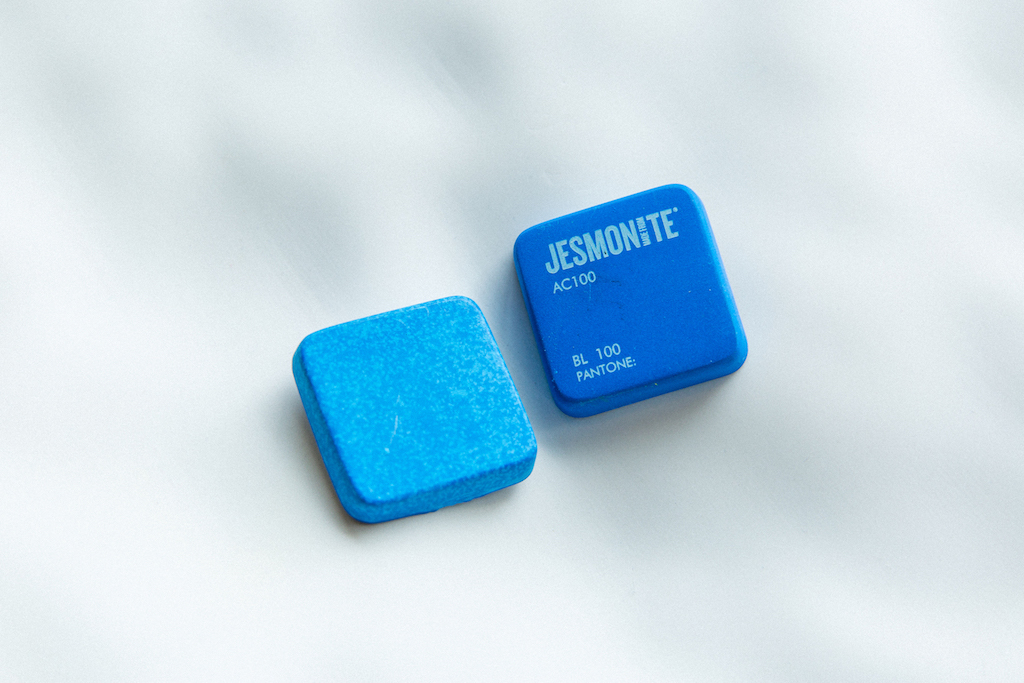
- Left: A unevenly colored sample filled with air bubbles. / Right: A beautiful bubble-free sample.
–It looks like white sauce. It seems like it’s better to use a larger container to make it easier to stir completely.
Matsumoto: Yes, exactly. When you’re finished mixing, you have to remove any bubbles before pouring it into the mold. Just like with cooking, you have to tap the container. If you look closely, you can see that there are tiny bubbles inside.
Matsumoto: I can see you’ve mixed it very well. Now it’s time to pour it into the mold. Tapering the mouth of the container makes it easier to pour. When it starts to harden, it will emit heat with a temperature of about 104°F (40°C). This gives it a warm surface similar to plaster.
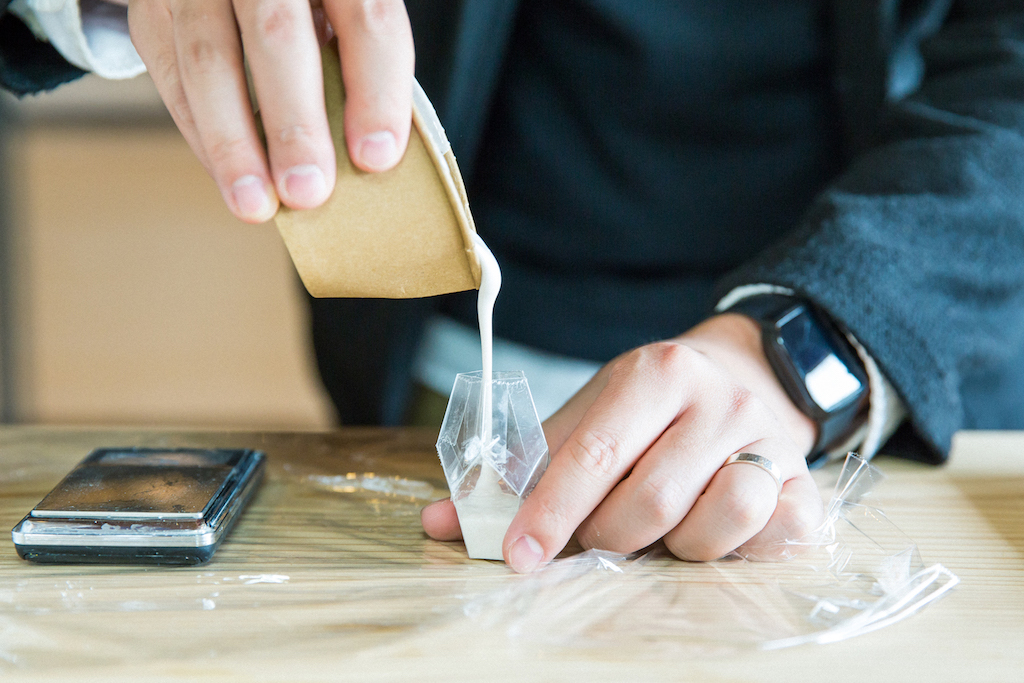
–Feeling a sense of warmth coming from an inorganic substance is a little strange. It’s sort of endearing.
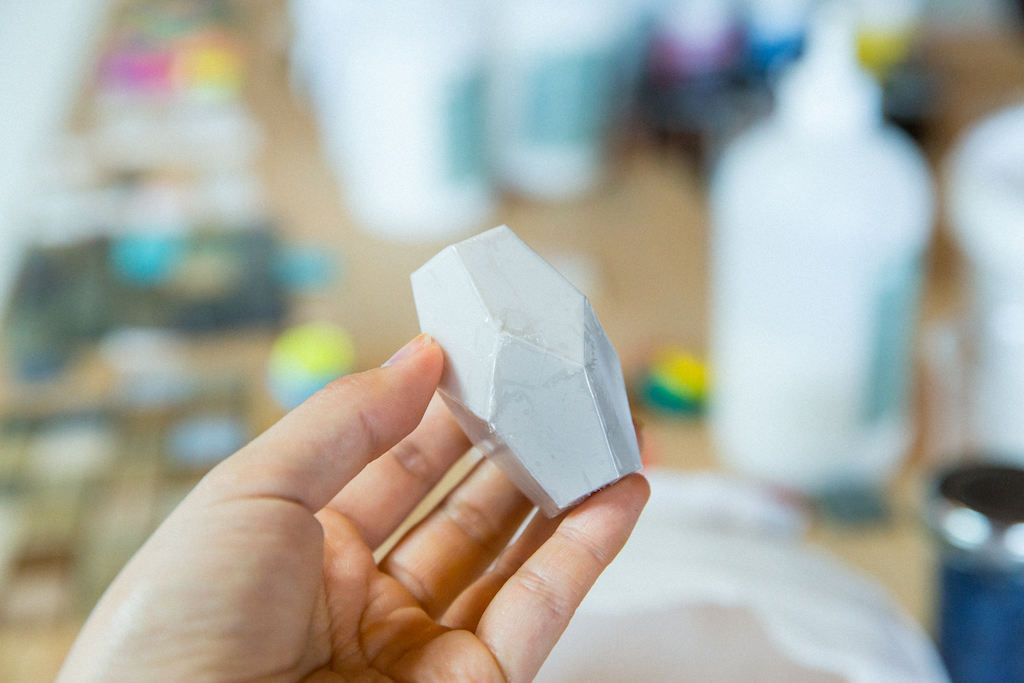
–Slowly but surely, our mixture has solidified throughout. Is there a recommended time to wait before taking it out of the mold?
Matsumoto: It’s best to let the mold cool off before taking it out so that the edges stay nice and smooth.
The hardening process starts in 10-20 minutes, but it takes 1-2 days for the material to reach its full strength. As such, treating the material after it’s taken out of the mold is handled on a case-by-case basis. If you want to shave off a large portion of it, it’s easier if the material is treated before reaching its maximum hardness. However, if you are mixing in metal, it’s better to treat it after it has completely solidified.
A wide variety of colors and textures for bringing out the creativity in you
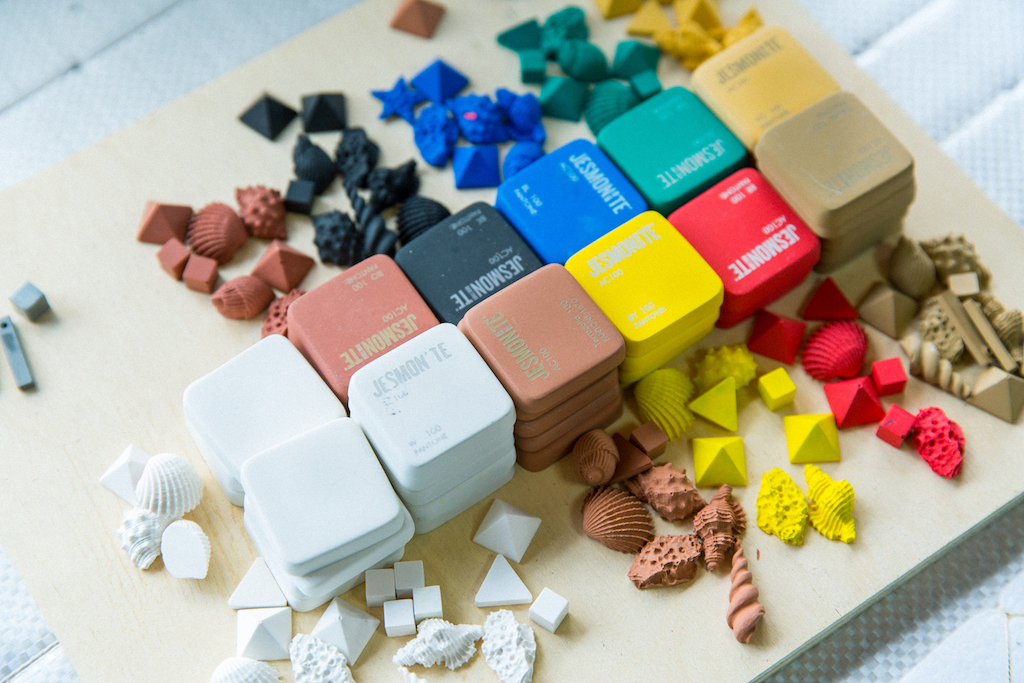
–Now let’s experiment with making our jesmonite exhibit some distinctive colors and textures. So how do you add color to your molded jesmonite?
Matsumoto: Jesmonite has a specially designed pigment that makes coloring very easy. The amount you add is up to a maximum of 2% of the jesmonite’s weight, so for 100g of jesmonite you would use 2g of pigment. If you exceed this amount, it can cause defects in the solidification process, so please be careful
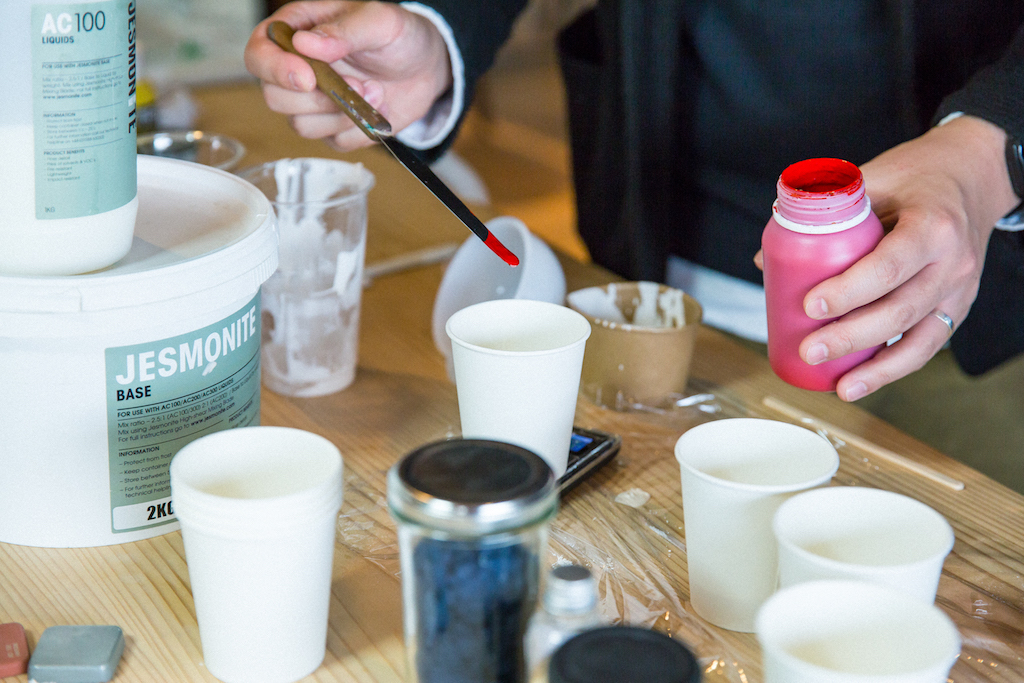
–It’s true; even the tiniest dose of pigment gives it a full coat of color.
Matsumoto: A spoon with a curved tip (similar to an ear cleaner) is a handy tool to have for this process. After stirring in the pigment, the rest is just a return to the basics.
Aside from mixing in the pigment, there are other coloring and painting steps that can be taken after the material hardens.
–So there are many different ways of adding color. Does this mean that you can use any type of paint to give it color?
Matsumoto: Jesmonite is a water-based material, so water-based acrylic paint is considered the best for it. However, after experimenting with a variety of different options, I have found that urethane and lacquer paints are also acceptable. Still, depending on the strength of the paint and thickness of the paint film, these paints may cause issues.
Also, when using oil-based paint, no surface preparation is needed. Ordinarily, surface preparation is an absolute necessity, but with jesmonite I have found that, when the solvent is not particularly strong, it is safe to paint the surface directly.
–That’s amazing! There are tons of creators struggling with surface preparation who would be thrilled to hear this. This is a great piece of on-the-job know-how.
–Looking at the samples you’ve made, I see can lots of different textures. Some are metallic, some rusted, and some have a green patina. Could all of these be made without any special techniques or experience?
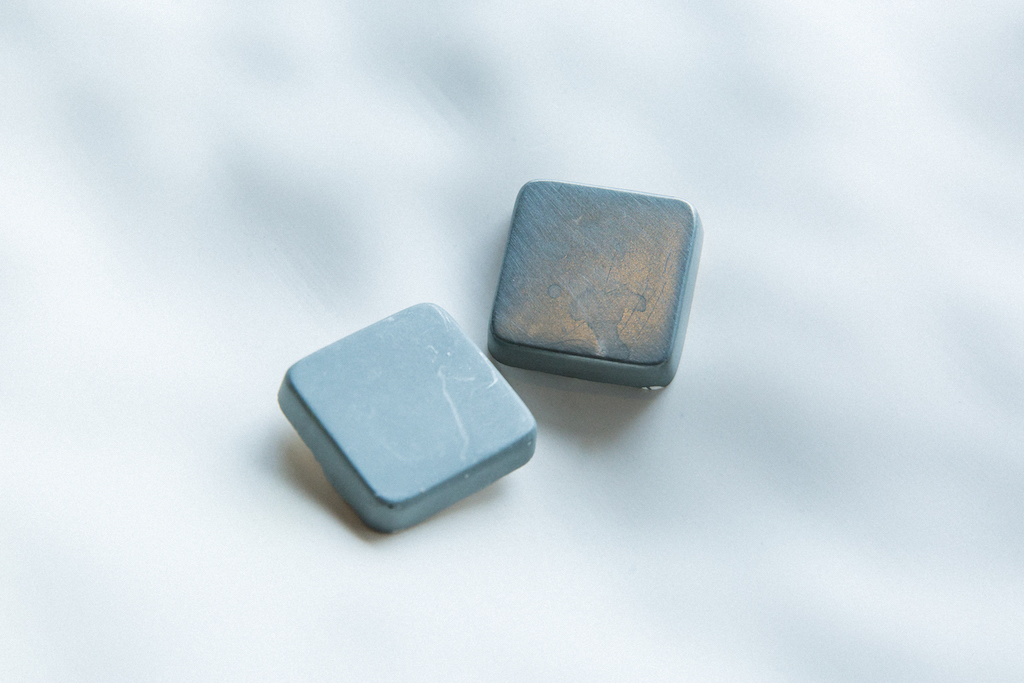
- Left: Jesmonite mixed with denim powder / Right: Silver bronze metal filler
Matsumoto: Yes, anyone could do it. You can add wood powder, mica, metal powder, and a variety of other materials to change its appearance. Just like when applying pigment, it’s better to mix the materials in before the hardening process, although there are also ways of simply adding it onto the surface.
–So jesmonite makes it easy to recreate textures that would otherwise be impossible for someone with no crafting expertise. With the ability to create a variety of unique textures that vary according to what material is mixed in, you could really have fun experimenting with a wide variety of materials.
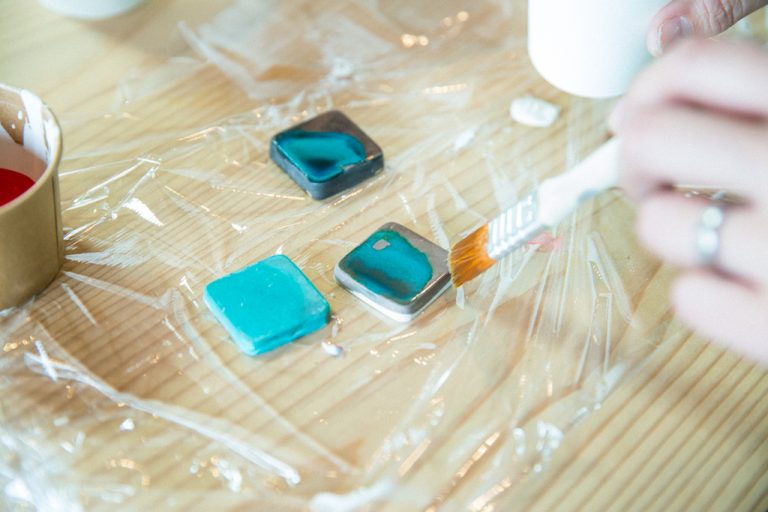
- Ammonium chloride painted over copper filler to exhibit a green patina.
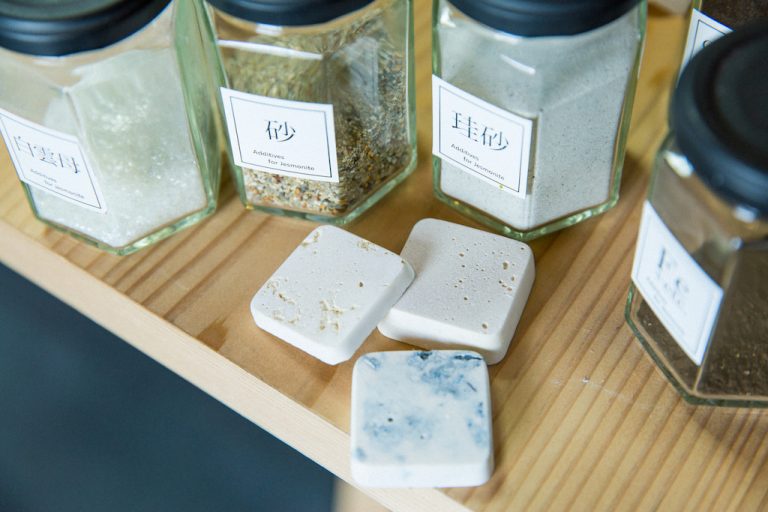
- Jesmonite can be mixed with various other materials such as sand and gravel.
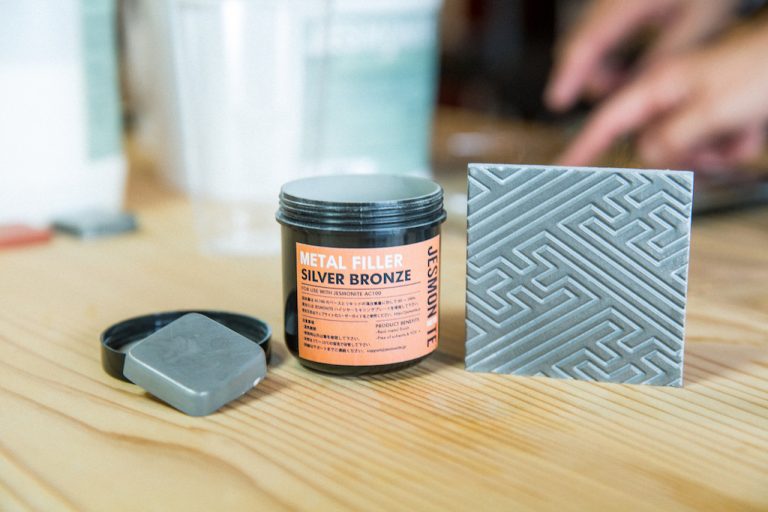
- A sample of jesmonite mixed with metal powder.
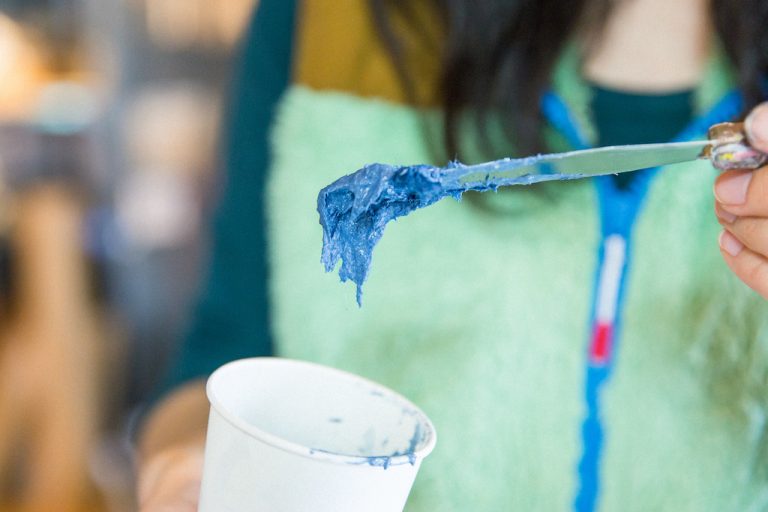
- Mixing with the dust created during the denim treating process created a highly viscous material.

- A hollow model of a cabbage made from a silicone mold.
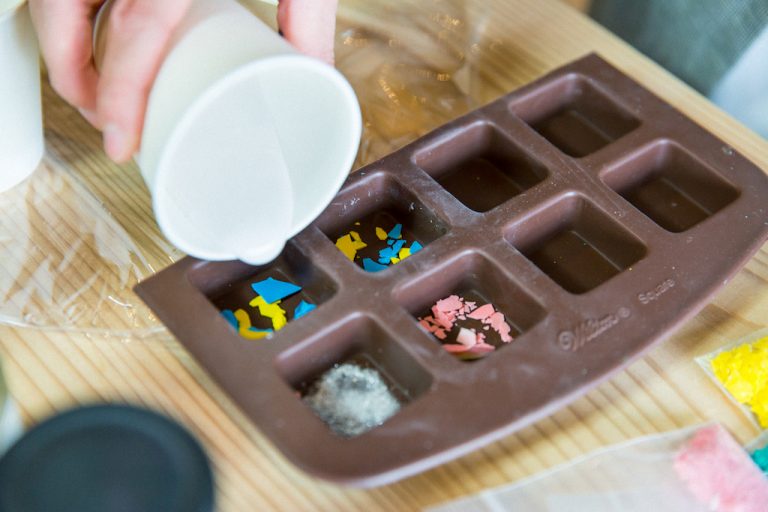
- When designing only a surface texture, spreading the material around the bottom of the mold creates a beautiful finished product.
Simple enough for a beginner to use, but able to exhibit complex textures
–We know that jesmonite is able to exhibit a range of different textures, but is it also water-resistant and/or fire-resistant?
Matsumoto: It does not repel water, meaning that you would have to use a sealer or special coating to make it water-resistant. Left as it is, jesmonite absorbs water like bisque pottery. If using it for a coaster, you could let the jesmonite’s natural absorbency do the work without having to coat it with a sealer.
It can withstand temperatures of up to about 212°F (100°C). It passes the fireproof test of the British Standards (BS) system, but this is only a basic architectural standard. Jesmonite cannot be used like a fireproof brick; it is not suitable for use in high-temperature environments.
Although it is difficult to mold something that can handle direct contact with fire, there are artists who use jesmonite to create objects such as lampshades and candle stands.
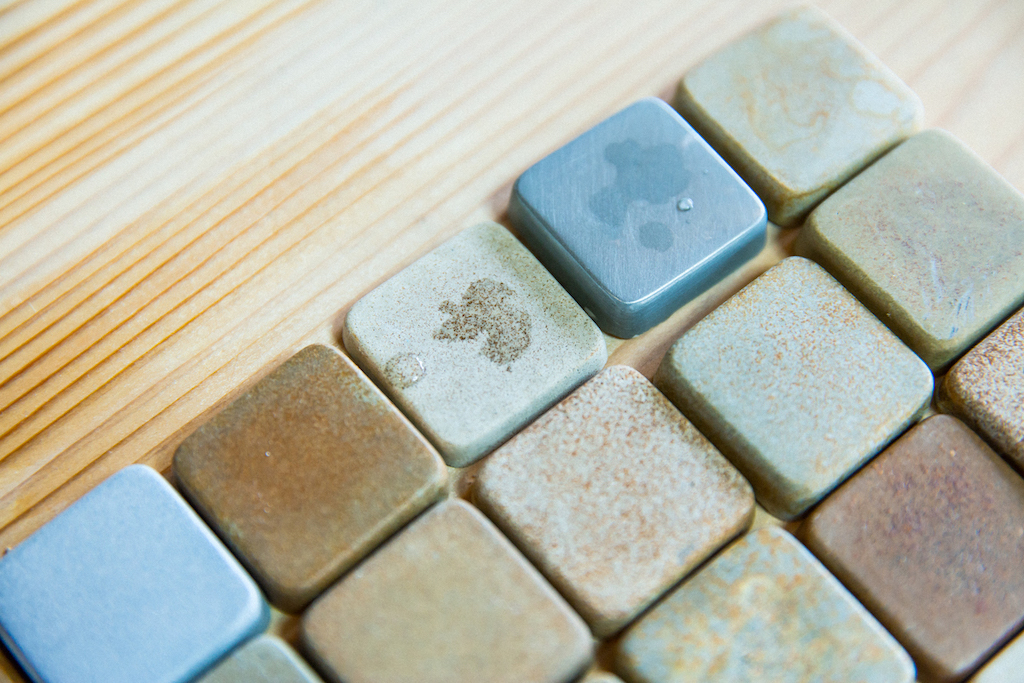
–How strong is jesmonite?
Matsumoto: If given some degree of thickness, it is not easy to break. If you want to increase the strength of a thin piece of molded jesmonite, you can use a type of glass fiber specially designed for use with jesmonite. Ordinarily, glass fiber is too prickly to carry without gloves, but this type of glass fiber is safe to touch with your bare hands. The fibers are long and flexible with very few loose glass fragments.
(*However, just in case, we still recommend wearing gloves in the interest of safety.)
–I always thought of glass fiber as being too dangerous to touch with your bare hands. That’s amazing! With it so easy to bend with just your hands, I can see how it could be freely manipulated to suit what you’re trying to make.
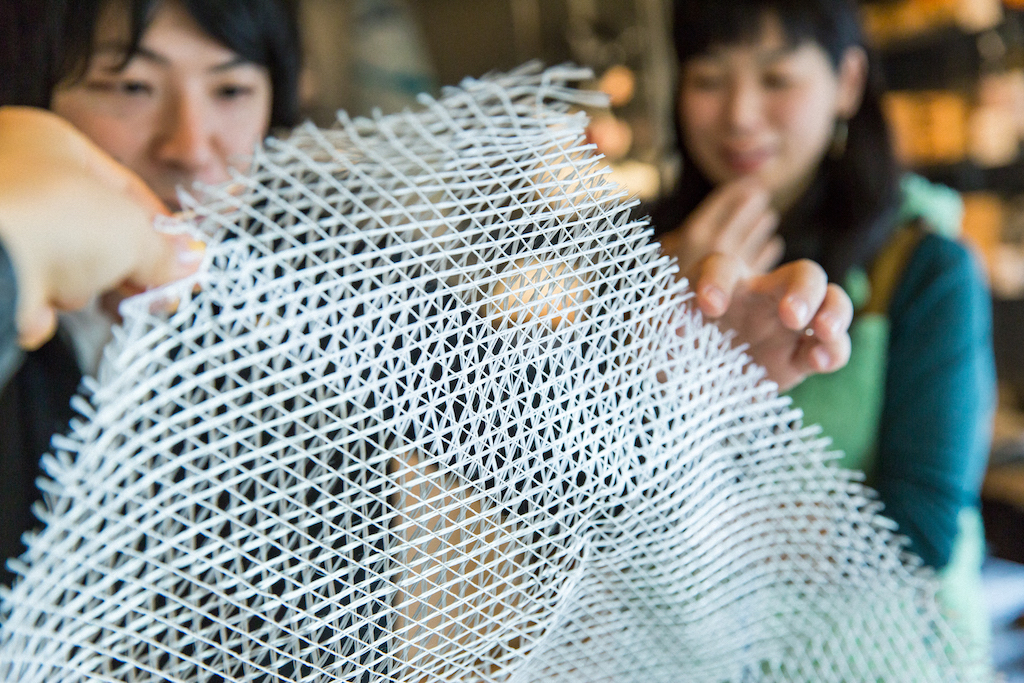
- Glass fiber for jesmonite molding
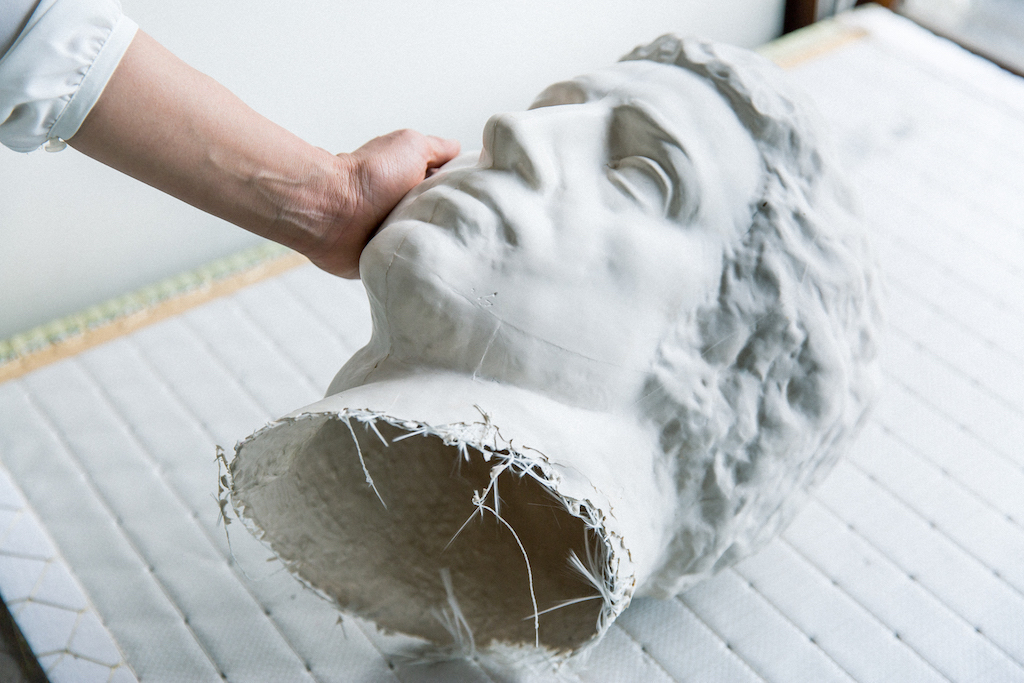
- A hardened jesmonite sculpture made with glass fiber
The perfect material for achieving ideal production quantities
–So far we have discussed the characteristics of and proper way of using jesmonite, and as far as I’m concerned, it is an absolutely dream-like material. You can both create objects with jesmonite itself and produce brand new substances by mixing in other materials. With the ability to take on many different appearances, it makes an absolutely first-rate base material. This really makes me want to drop everything and start inventing new and interesting textures.
Matsumoto: Thank you, but the advantages you’re describing could also be called defects. When it comes to incorporating jesmonite into your products, you might be paralyzed by the endless list of things you can do with it and have no idea what method to adopt. Even if you aim to produce a steady rust or patina texture, there may be no one able to handle the manufacturing from an industrial standpoint. The distinctive strengths of jesmonite could be viewed as both advantages and disadvantages.
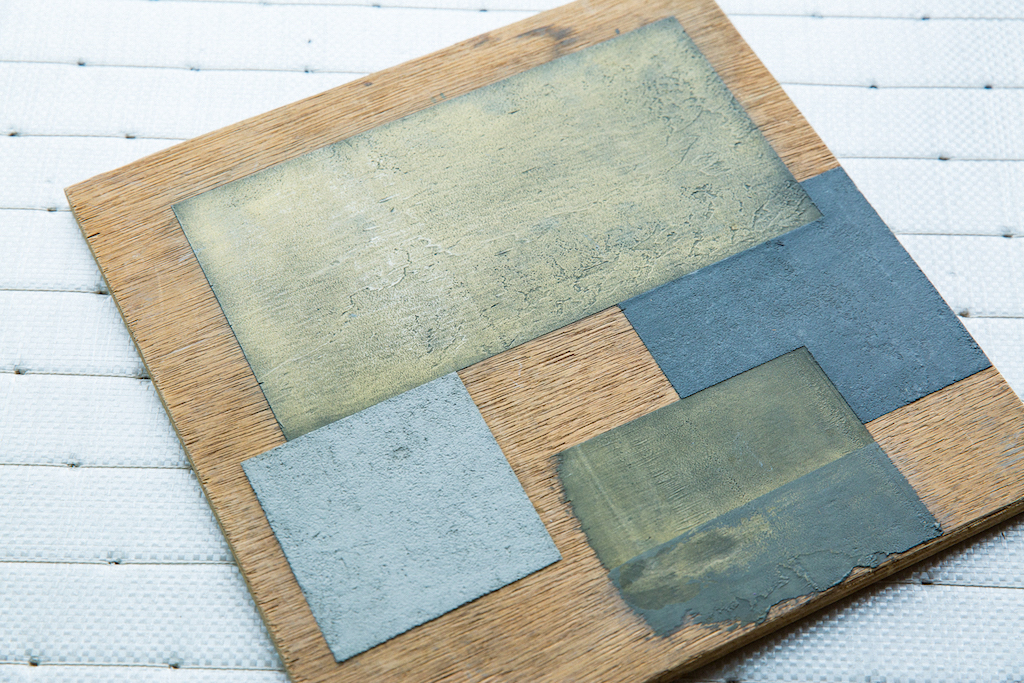
- Samples of jesmonite on a wooden board showing a variety of textures, including cement and metal.
–Mass production at machine-like rates is a challenge, but when using a mold, you can make what are essentially handmade objects in reasonable quantities, which does have a certain appeal.
Traditionally, the crafting industry has been polarized between the idea of producing architecture, products, and other items in large quantities using mass supplies of industrial materials versus with high attention to detail and quality at the hands of a single person. However, while one-off products are not financially viable, there is still absolutely the need for products that are made with careful attention to detail. For example, select shops with locations all over the country are desperately in need of ingenious materials that can be produced on a semi-mass scale and are capable of exhibiting textures that exude originality, such as when they want to establish an original design store.
Matsumoto: While buying metal molds without mass-producing is not worth the expense, with 3D printers you can produce your own models and molds and then reproduce your product using jesmonite or a replacement material. With a few hundred dollars you can create your molds and earn a profit even without mass-producing, making this perfect for generating small to medium lots of a unique product.
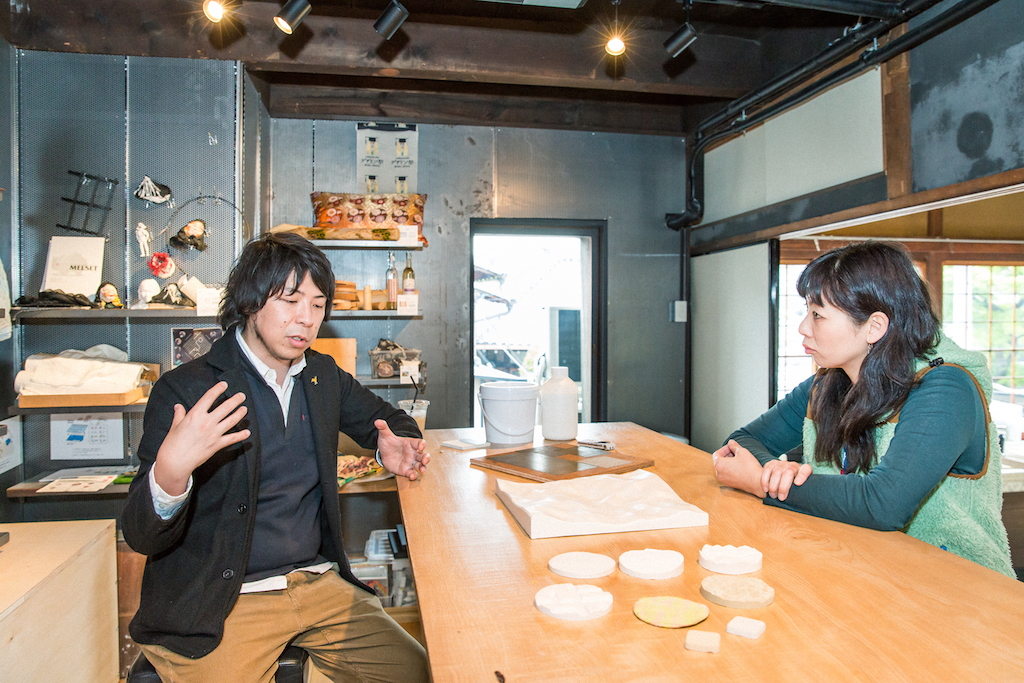
–Even without reaching full mass production, being able to give each product a different appearance and texture is definitely an appealing prospect.
With 3D printers, it’s becoming easier and easier to create any shape you can think of, but changing a material’s texture or surface appearance is not so easy. If you try to recreate a design using an algorithm, it will look like you’ve just created duplicates of something. When it comes to incorporating something natural into your product, you have to go through a process of trial-and-error. That being the case, it seems to me that jesmonite and 3D printers are two very compatible creations; they’re absolutely perfect for each other.
Matsumoto: Even without large-scale investments or equipment, you can still produce small to medium lots by hand. You can design textures and surfaces (i.e. stone patterns that require no special coating or metal cold casting) with more interesting appearances than the FRP of the past. I believe that jesmonite is a material that offers creators and artists everywhere a world of new possibilities.
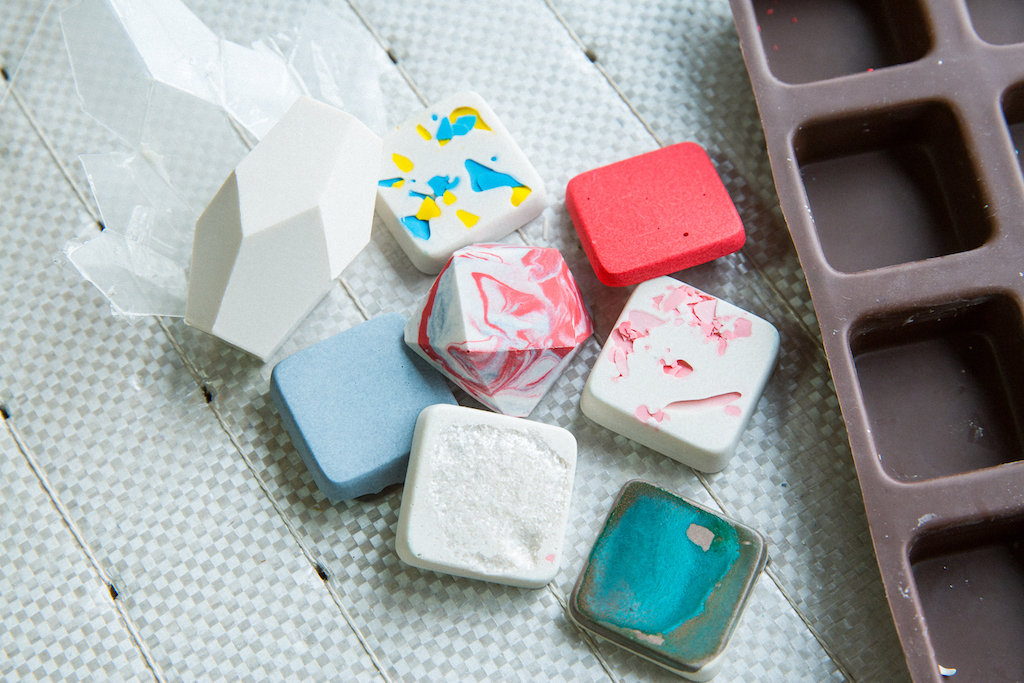
–With moderate production amounts, you can add value to each individual product design and avoid getting roped into cost competition, allowing you to increase the final unit price. Being able to sell a high quality product at a respectable price is very important, wouldn’t you say?
Giving products textures and surface appearances that can’t be achieved digitally or in a mass-production factory is an absolute blast. Even if you have no prior experience with resins, the water-based material jesmonite makes it very easy to start creating. Jesmonite seems like the perfect material for aspiring craftsmen to use in taking their first step towards becoming creators. Thank you for everything, Ms. Matsumoto!
(Writing: Yui Kitagawa / Photo: Hanako Kimura)
Profile
JESMONITE® Distributor Japan agency, C&B
Hiroko Matsumoto
Captivated by the possibilities presented by jesmonite’s strength and reliability, [[[Jesmonite Japan Distribution]]] has been selling jesmonite in Japan since December of 2016. As the head of the jesmonite promotion in Japan, Matsumoto disseminates information about the material to craftsmen everywhere. She also conducts workshops that invite artists, arts educators, and arts-focused university students to experience jesmonite’s textures, colors, and durable construction firsthand.
https://jesmonite.jp/
MTRL KYOTO・FabCafe Kyoto Manager
Kosuke Kinoshita
After graduating from Kyoto Prefectural University, I worked as a manager at the cafe “neutron” · art gallery “neutron tokyo”. School utilization facility “IID Setagaya Monozukuri School” is responsible for creators’ workshops and exhibitions, and collaboration with companies, schools and local governments. Joined Loftwork 2015 in charge of “MATERIAL KYOTO” to open from the fall of 2015. Under the motto of “creating an open and realistic place”, he is actively working as an “intermediary” promoting exchanges and emergence beyond regions and specialized fields.
Recent Articles
-
Interview
Creating the “New Normal” for the Future: What is the “Complexity” Necessary for Co-Creation Between Academia and Industry? An Interview with Professor Kouta Minamizawa (Part Two)
-
Exploring New Realms of Design with Academia – An interview with Professor Kouta Minamizawa about the potential of co-creation projects with Academia -(Part One)
-
REPORT:School of Fashion Futures